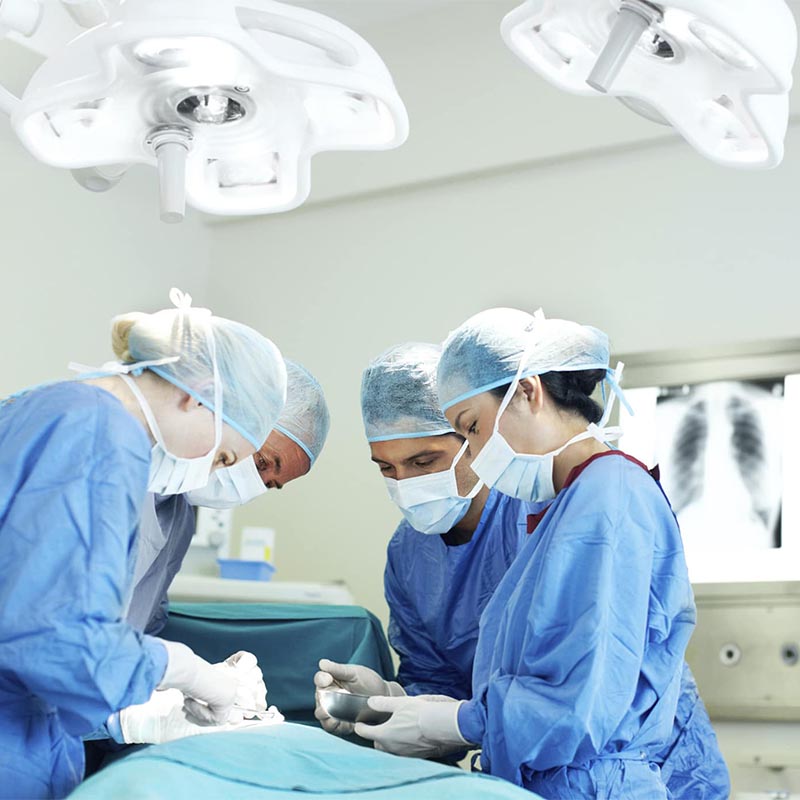
Biocompatibility
Before any material contacting human tissue can be used in a medical device, it must be evaluated to ensure that the chemical make up of the material does not cause damage to cells within the body. Liquidmetal has gone through several biocompatibility tests to confirm it is suitable for surgical instruments.
Surpassing the capabilities of Steel and Titanium
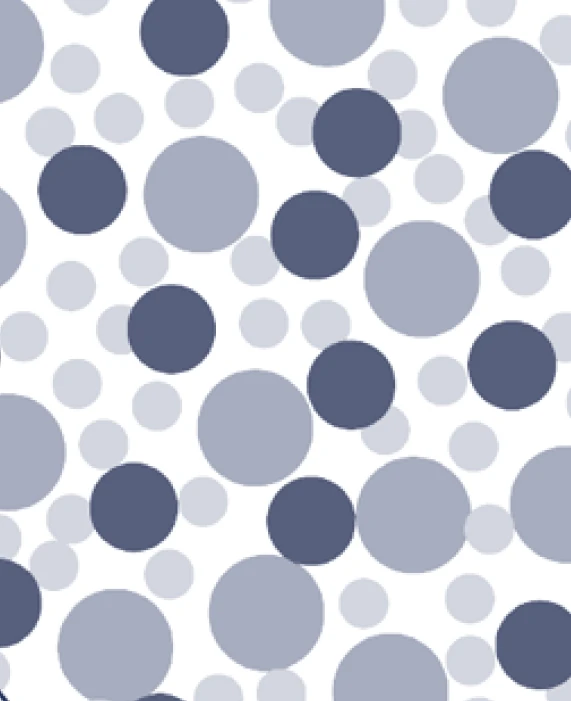
Liquidmetal®
Atomic Structure
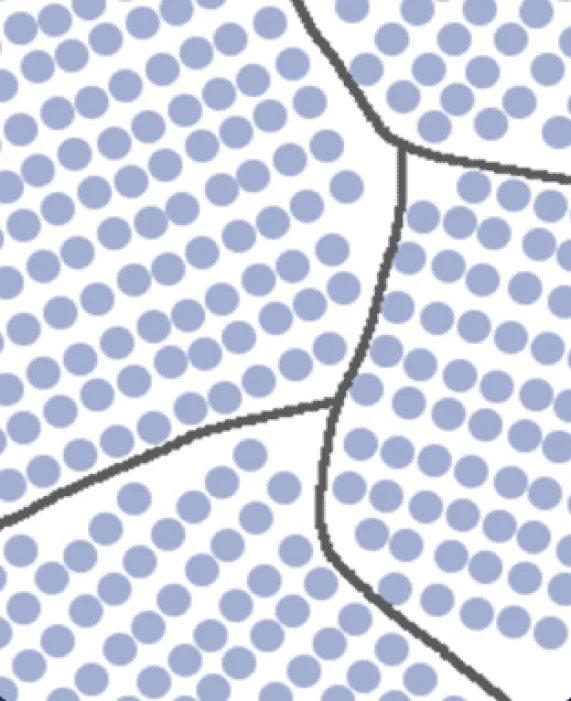
Crystalline
Atomic Structure
Typically, when a metal cools from a liquid to a solid, the atoms arrange themselves and grow into organized structures called grains. Where these grains intersect, a boundary is formed.
Liquidmetal was formulated to frustrate the movement of the atoms into the organized grain structure as the alloy cools. This results in a liquid-like atomic structure.
Metals and alloys get their strength from the atomic bonds within the material. These bonds are weakened across a grain boundary due to dislocations and impurities. Liquidmetal does not have grain boundaries, so it is atomically stronger than other alloys.
End Effecters
Jaw Grasper
Reduce tissue damage. Molded teeth eliminate sharp edges. Flatness and elasticity maintain consistent pressure down the length of the grasper to avoid pinching.
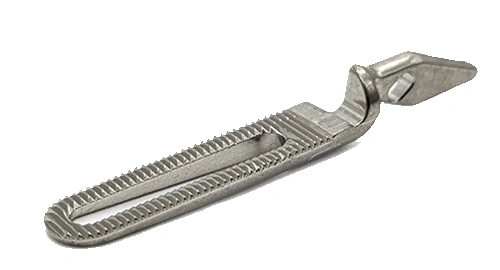
Clip Applier
The molding process gives new design freedom with features and precision that can’t be achieved with stamping.
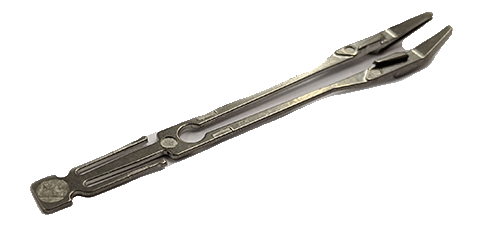
Staple Anvil
Precisely formed pockets and incredible flatness results in better staple formation and reduced bleeding at the staple line.
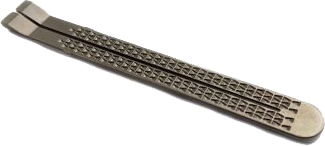
These are the parts at the end of the instrument that are interfacing with human tissue during a surgery. They need to be strong and durable to perform their task and they have intricate features requiring high precision. Examples of these parts are Jaws, Staple Anvils, and Clip Appliers. When used in minimally invasive surgeries, they enter the body through incisions as small as 5mm, so these are powerful parts in a small package.
Designers come to us looking for an alternative method of manufacturing these components to reduce cost. Common methods they want to replace are CNC Machining and Powder Metal Injection Molding (MIM). CNC machining is very costly and time consuming. MIM parts can be inconsistent and many times they need extensive machining to meet specification after molding. The precision of Liquidmetal injection molding can reduce or eliminate costly CNC processes and provide the features you need directly from the mold.
Liquidmetal also has the mechanical properties to meet and exceed the performance of materials that are commonly used today. It is stronger and harder than both Stainless Steel and Titanium, and it has these properties right out of the mold, without heat treating. Liquidmetal also molds with a smooth surface finish, so additional polishing or coatings are not necessary.
Bezels and Housings
Contoured Geometries
Minimal shrinkage allows for complex shapes in 3 dimensions. Create a durable hand-held device with an ergonomic feel and pleasant cosmetic finish.
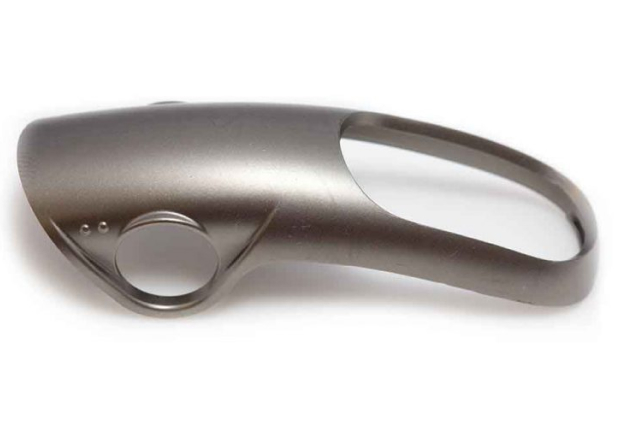
Electronics Bracket
Thin wall molding to replace expensive machining and maintain incredible strength. Non-magnetic property does not interfere with sensitive electronics.
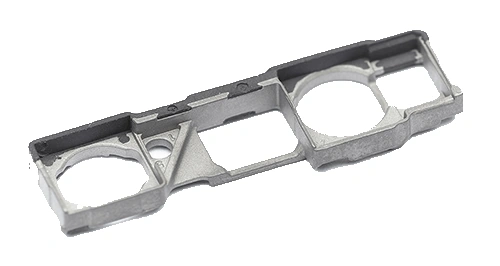
Molded Housing
Protect internal components with a unique elasticity that cannot be dented. Eliminate extra fasteners and reduce assembly time with integrated clipping features.
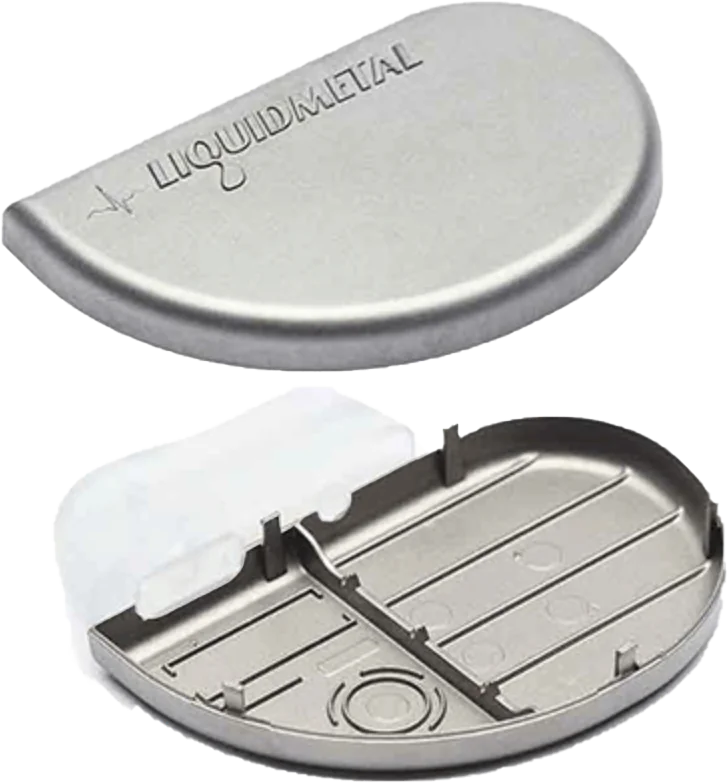
Liquidmetal is more durable and cosmetically pleasing than a molded plastic. It can be molded into complex contoured geometries like a plastic, and it cannot be dented. That is a feature of being an amorphous metal. Liquidmetal is also very hard, which is desirable for scratch resistance. It is a non-magnetic alloy, making it suitable for use in an MRI environment.
There is also a big advantage to molding housings that contain electronics and optical components. These housings would be very expensive to machine out of a block of raw material. Liquidmetal can mold all the features in one step with the precision to properly align to mating components. Liquidmetal can also be over-molded with plastic and Silicon for applications that have such requirements.
Drive Mechanisms
Non tissue contacting components within the handle of a device are also good candidate parts for Liquidmetal. Compact strength is needed in a tight package for levers, gears, and rack and pinons. With Liquidmetal, you can mold levers within the contoured geometry of a handle to fit the form of an aesthetically pleasing hand. Gear teeth can be molded directly into a drive mechanism without any complicated machining, and the surface finish is so good, that you can avoid grinding, polishing or coatings to get a nice smooth and predictable function.
Molding with Liquidmetal also allows you to combine multiple parts into one. Let’s say you need a pinion. Rather than making a gear and press fitting a pin into it, you can mold both components together to improve the strength and improve the precision of its concentricity. It’s not uncommon to replace a plastic part either to increase the strength and durability.
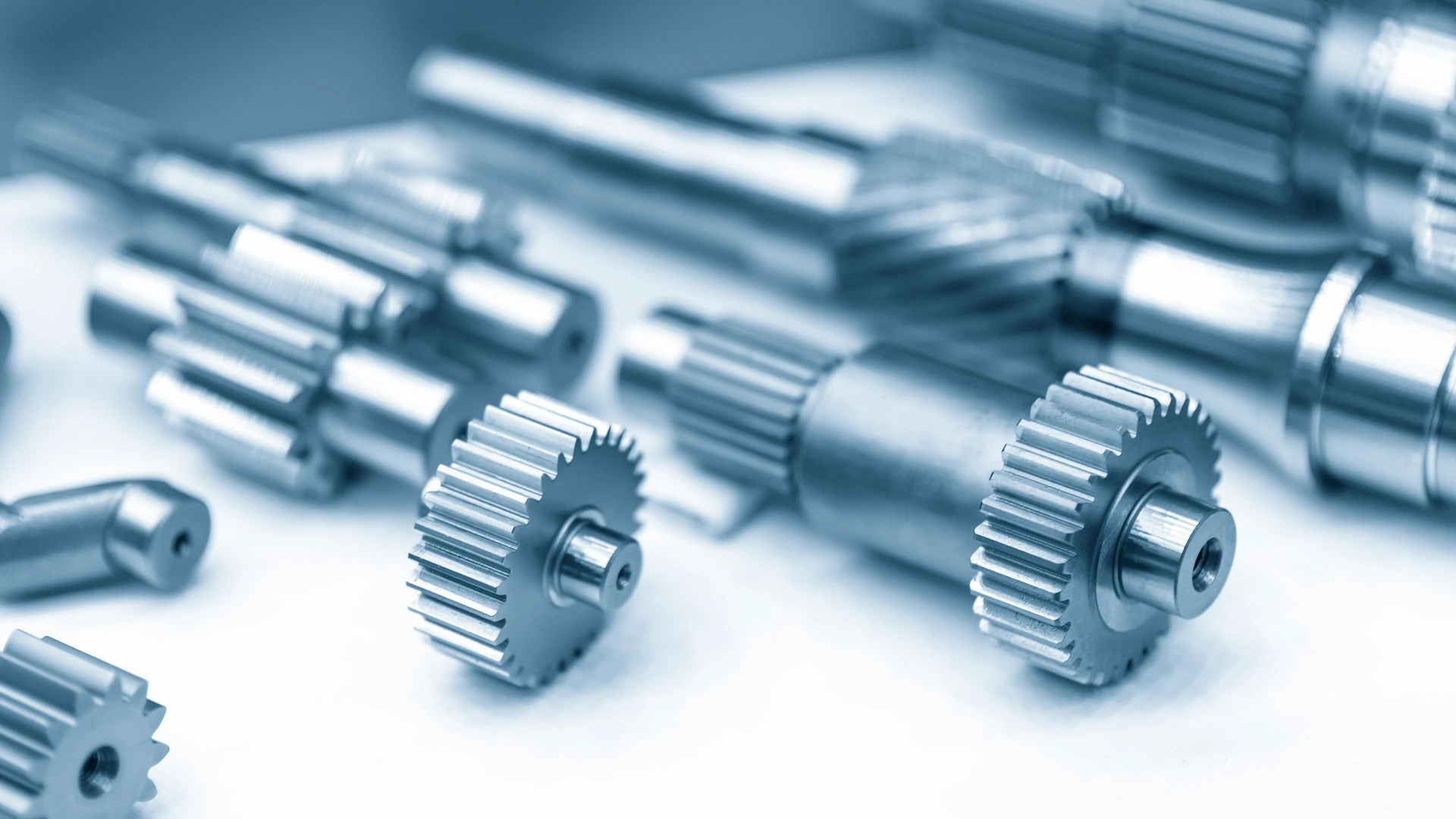