Process Comparison
When selecting a manufacturing process, it’s crucial to carefully consider your specific needs. Each method offers distinct advantages and trade-offs.
Metal Injection Molding (MIM) is a good choice for small components with low complexity produced at scale. CNC machining excels in complex shapes with tight tolerances, particularly for smaller production volumes. Liquidmetal’s Bulk Metallic Glass (BMG) process provides a unique opportunity to provide both high accuracy precision and the ability to scale at high-volume production.
Process Considerations
It is advantageous to reduce the number of manufacturing post processes required to produce a finished part. This will reduce development time, and maximize yield rates once in production.
Liquidmetal’s net shape molding allows you to check critical dimensions right out of the mold. A MIM part cannot be measured until after several post processes. This can result in substantial scrap and time lost if there was a problem upstream. These manufacturing trade-offs may be offset by part cost and the speed at which you can make parts in high volume.
Metal Injection Molding
(MIM)
Mixed Polymer and Alloy
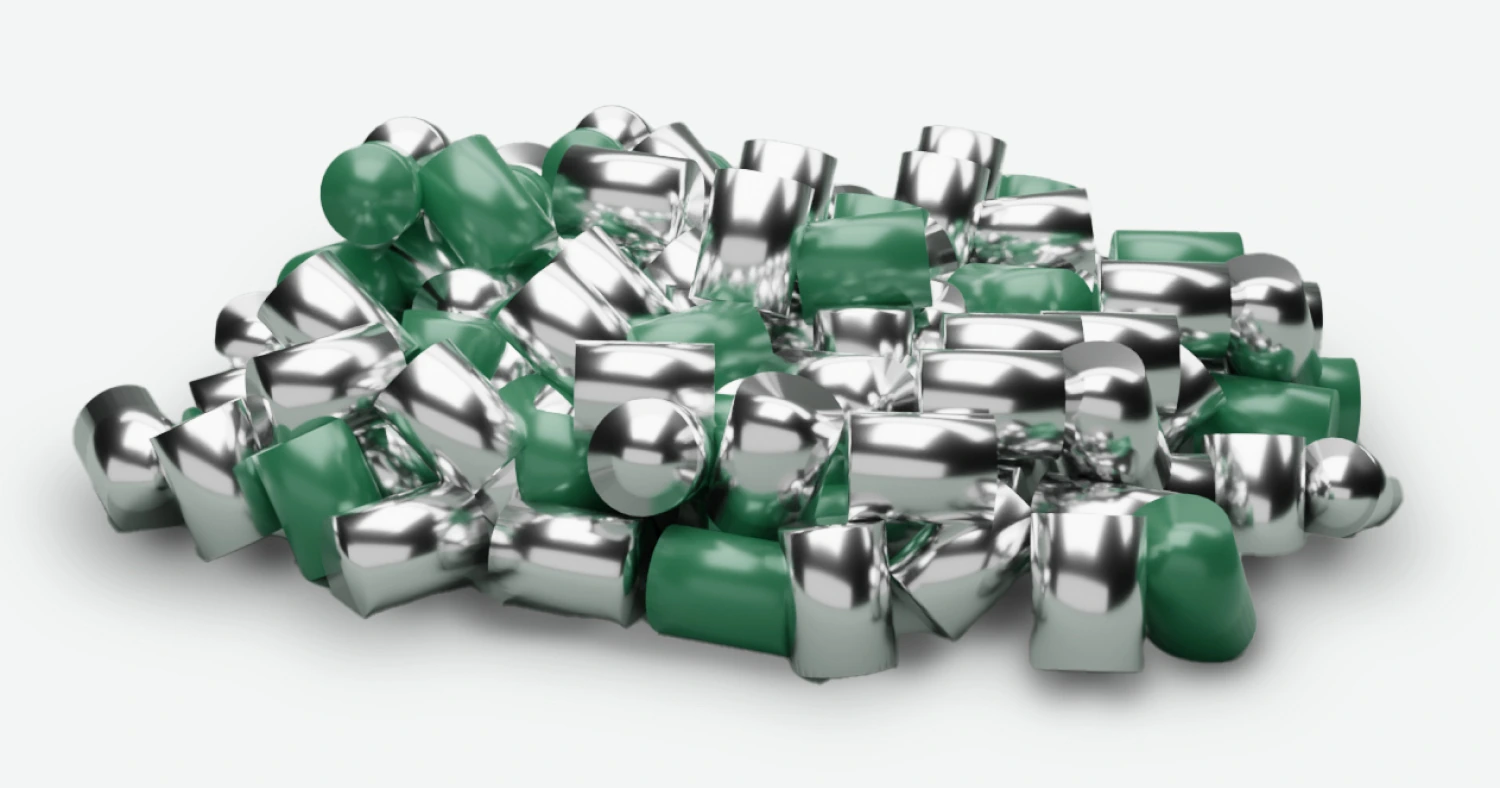
Injection Molding
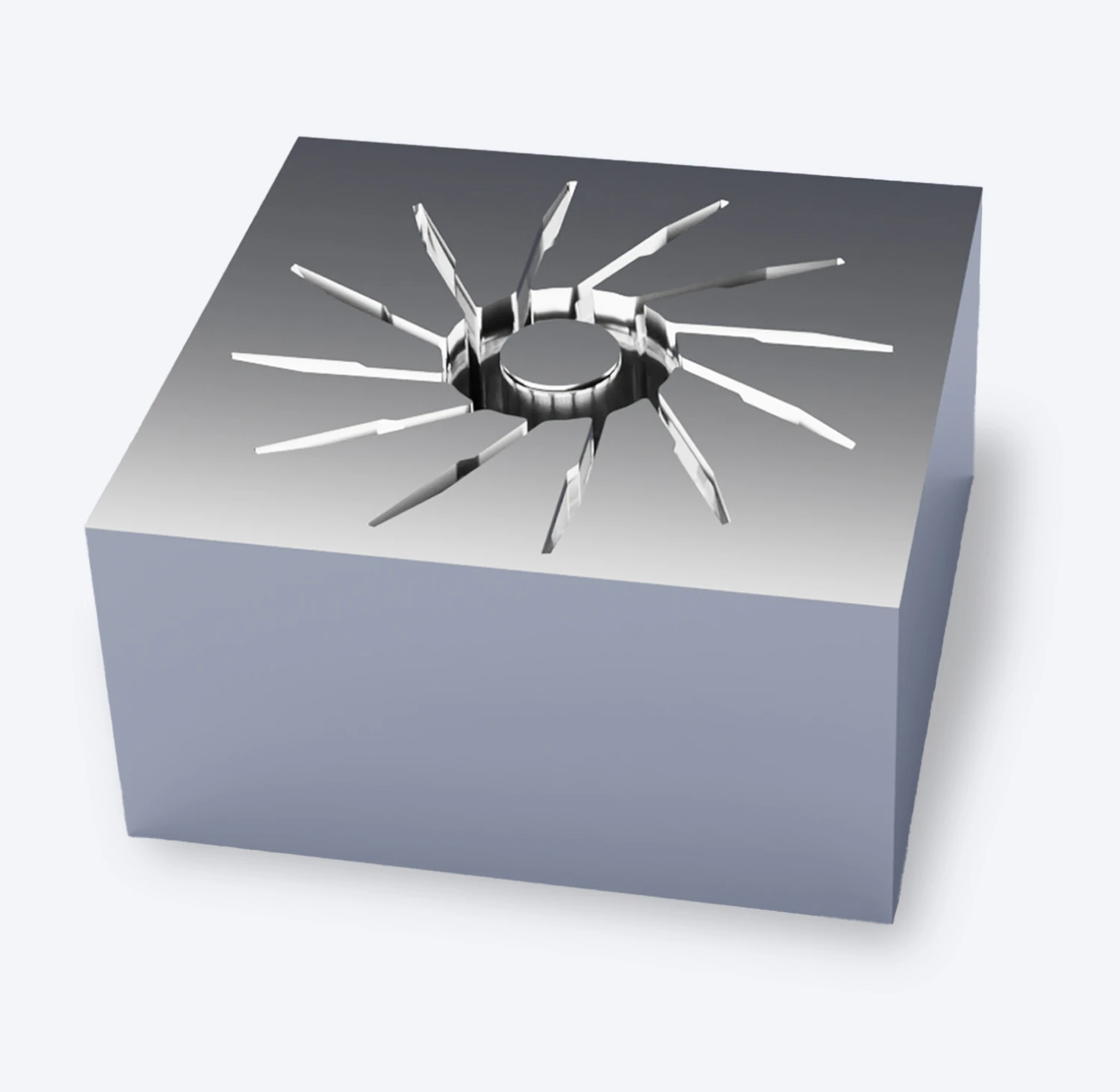
Green Part
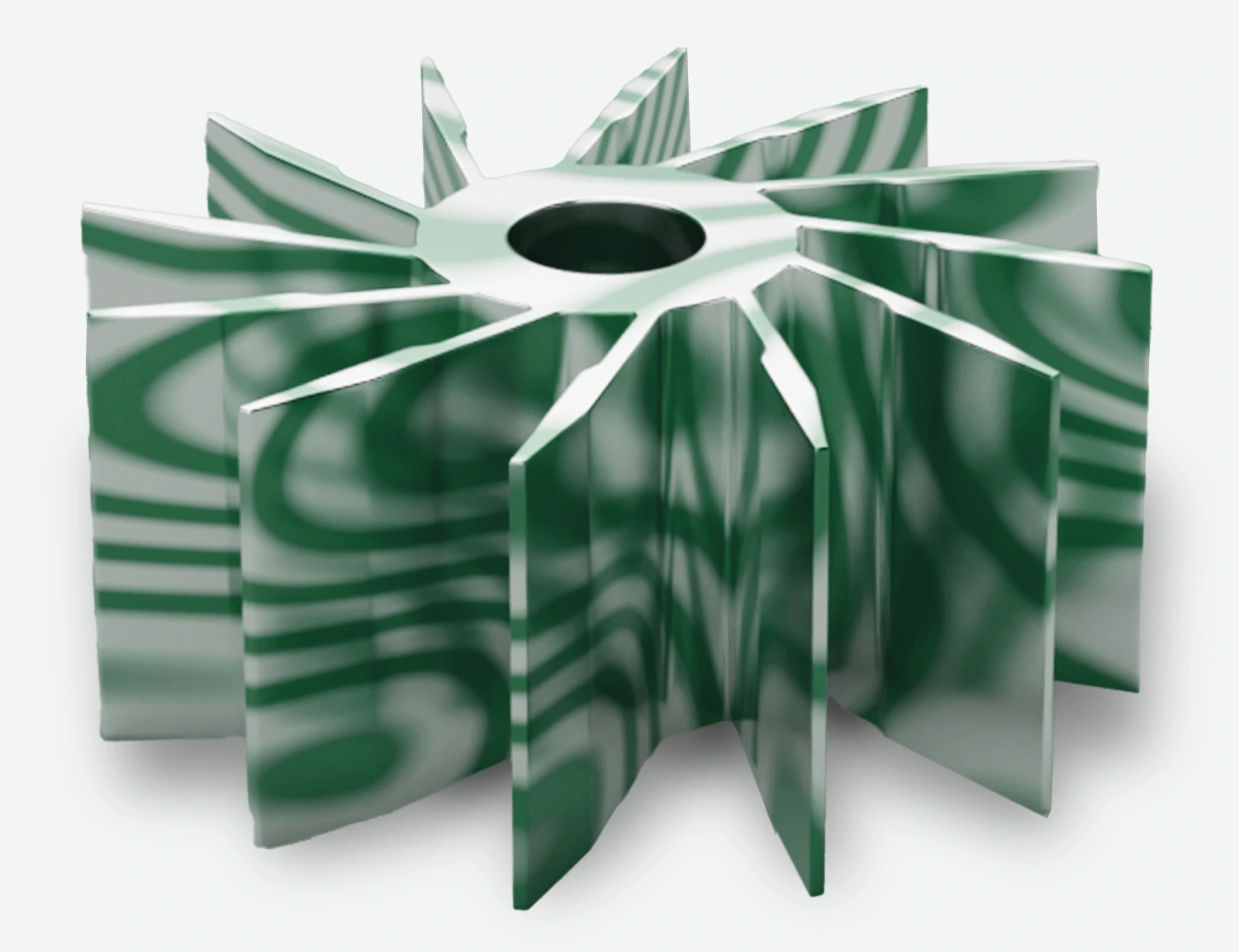
De-Binding
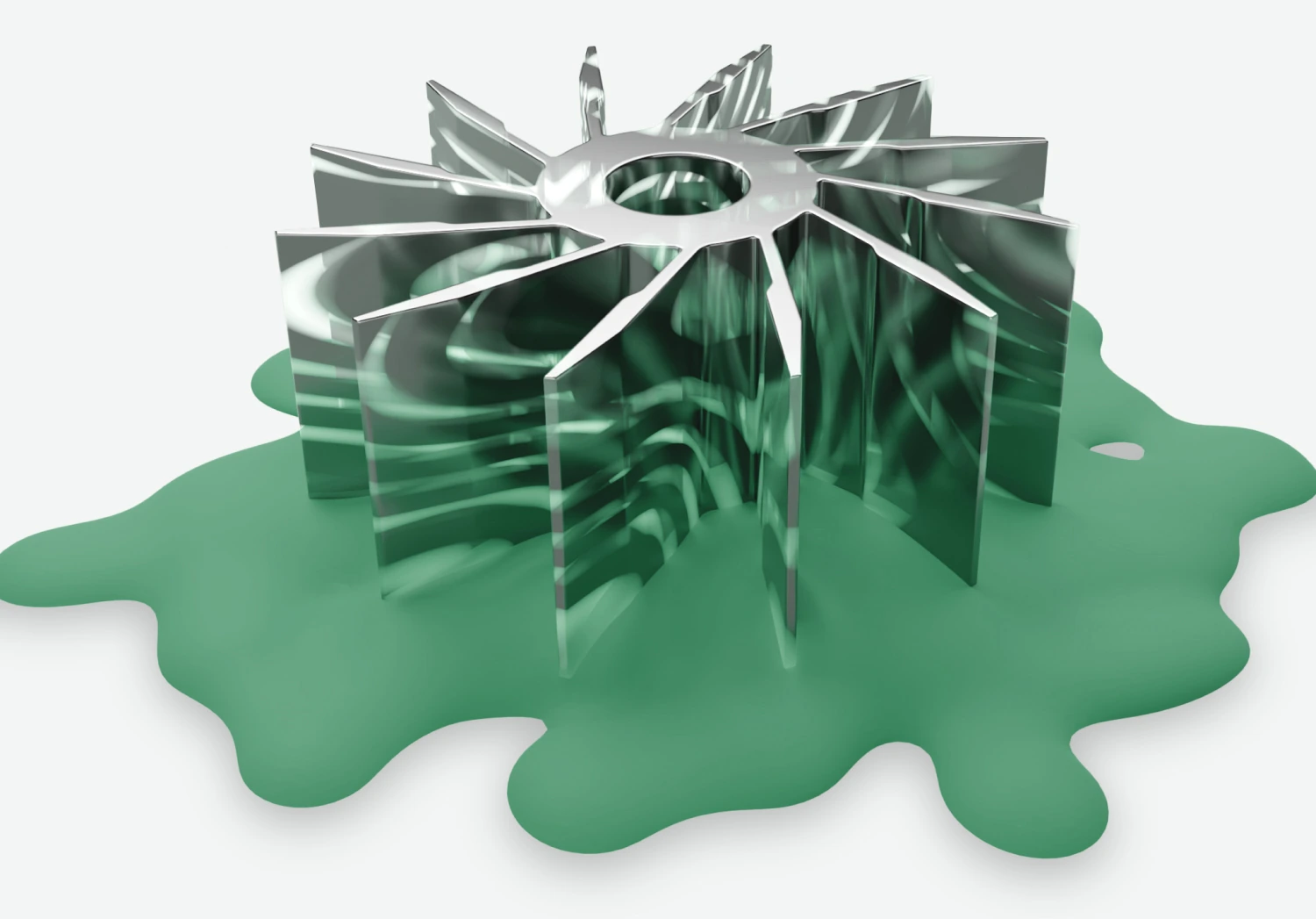
Sintering (20% shrinkage)
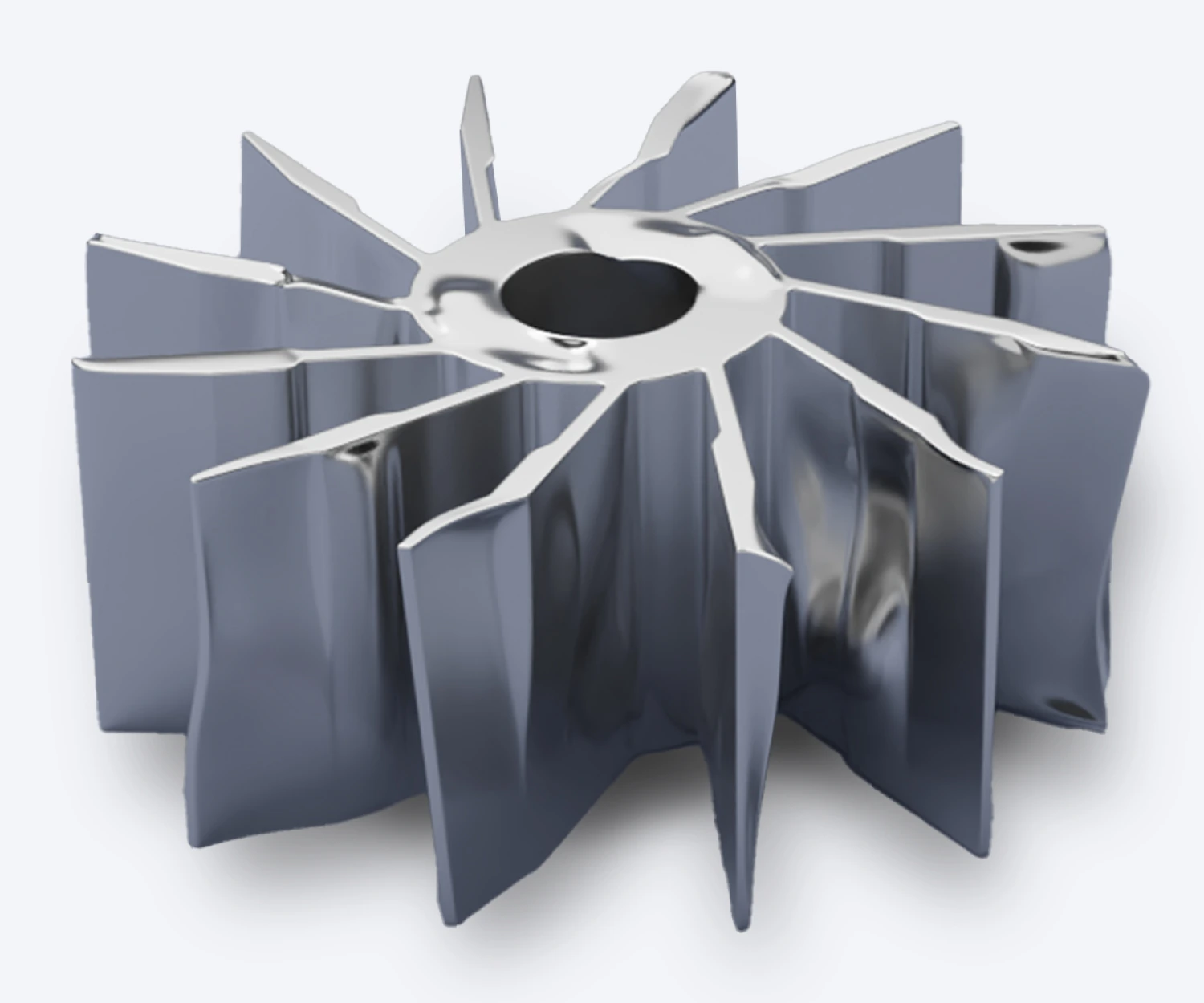
Coining Finished MIM Part
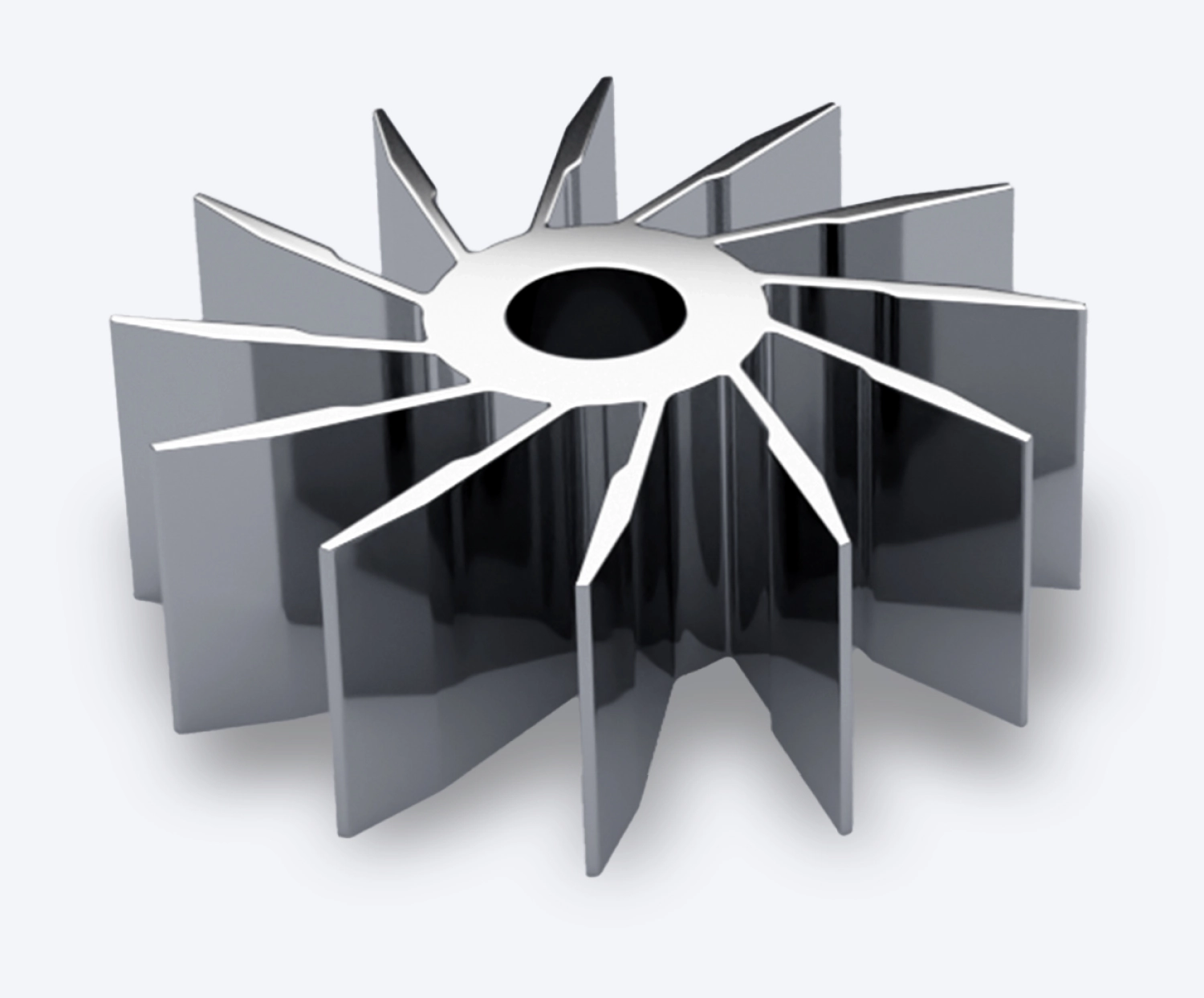
Conventional Machining
(CNC)
Block Alloy
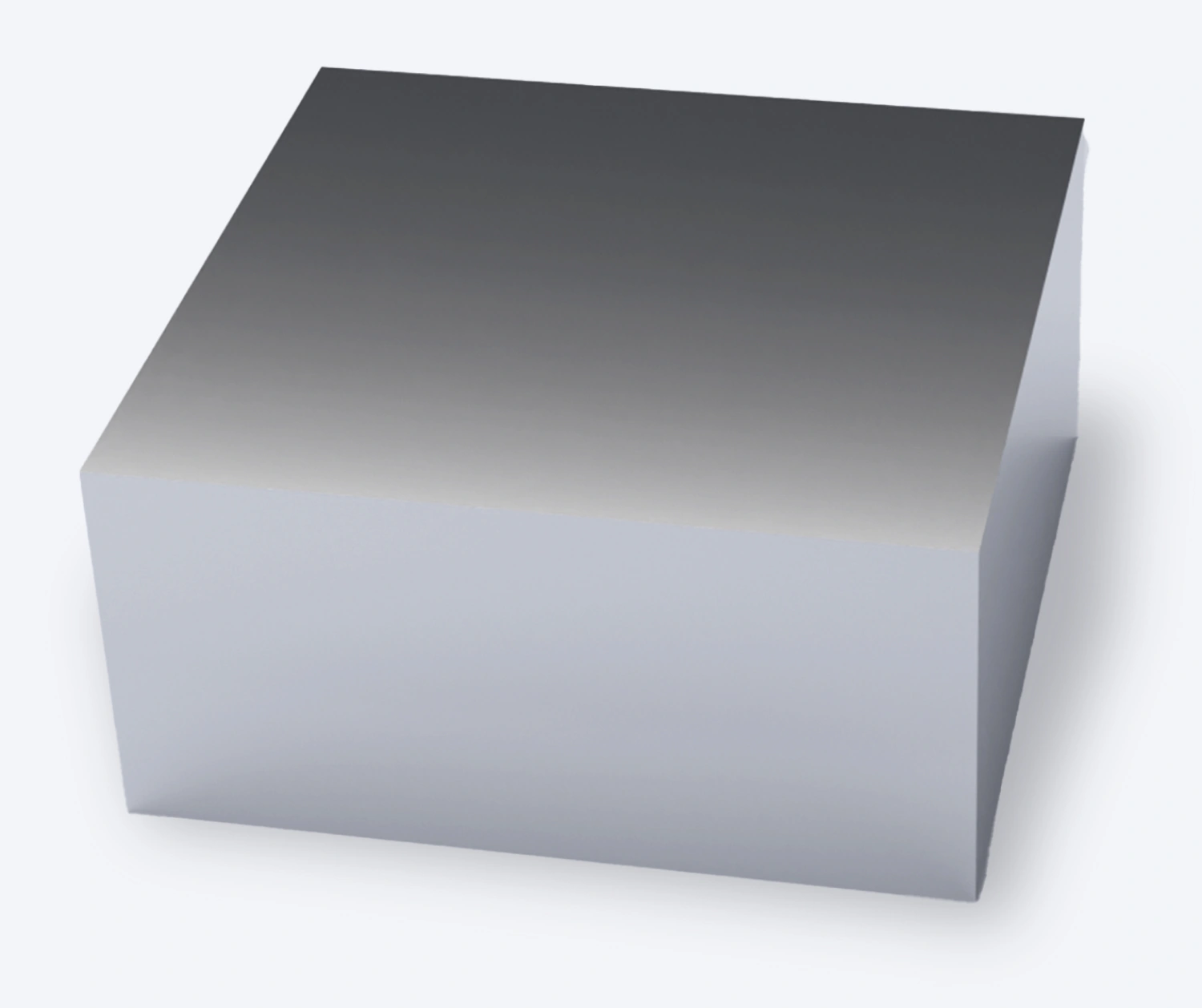
Machining Op 1
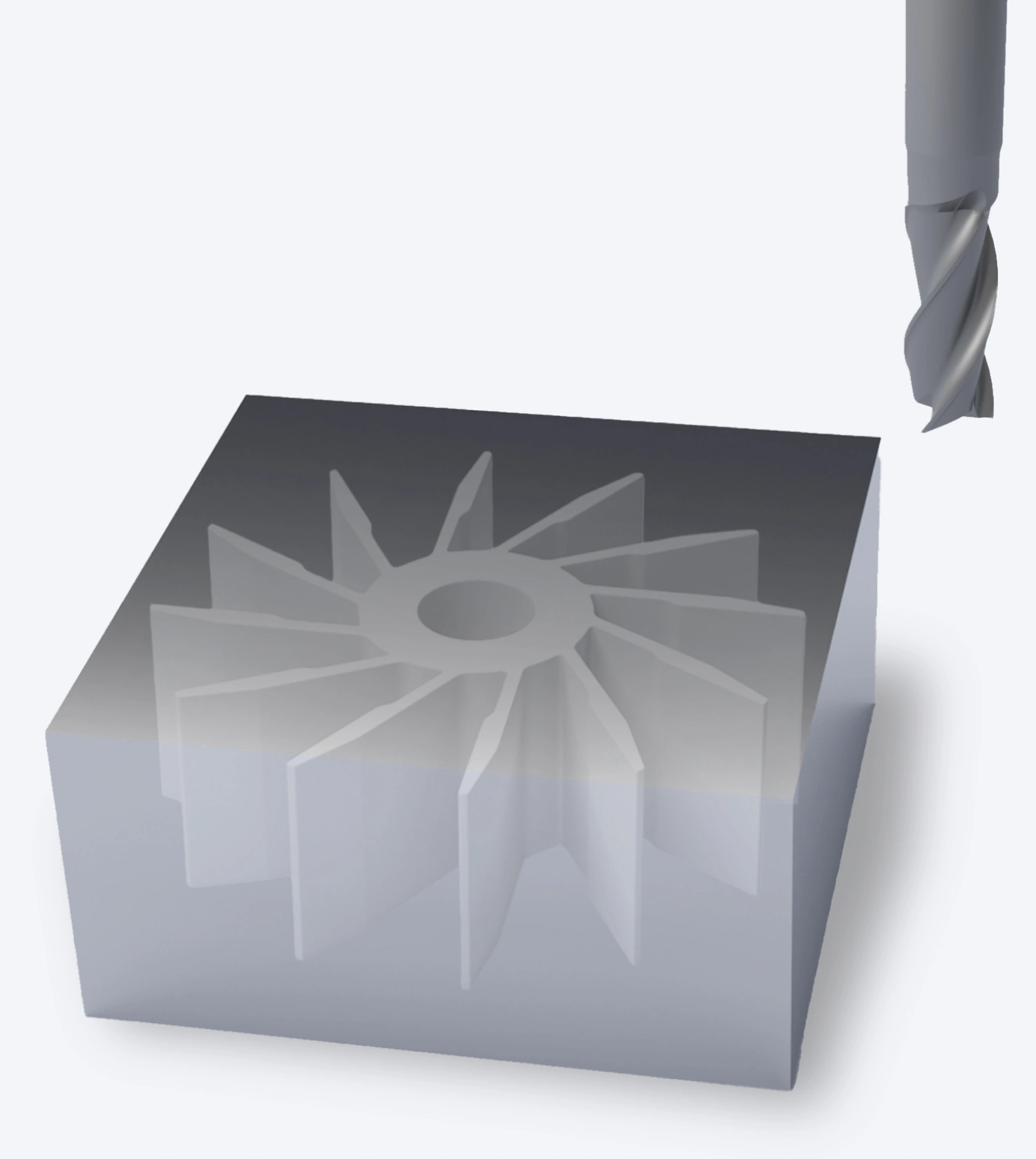
Machining Op 2
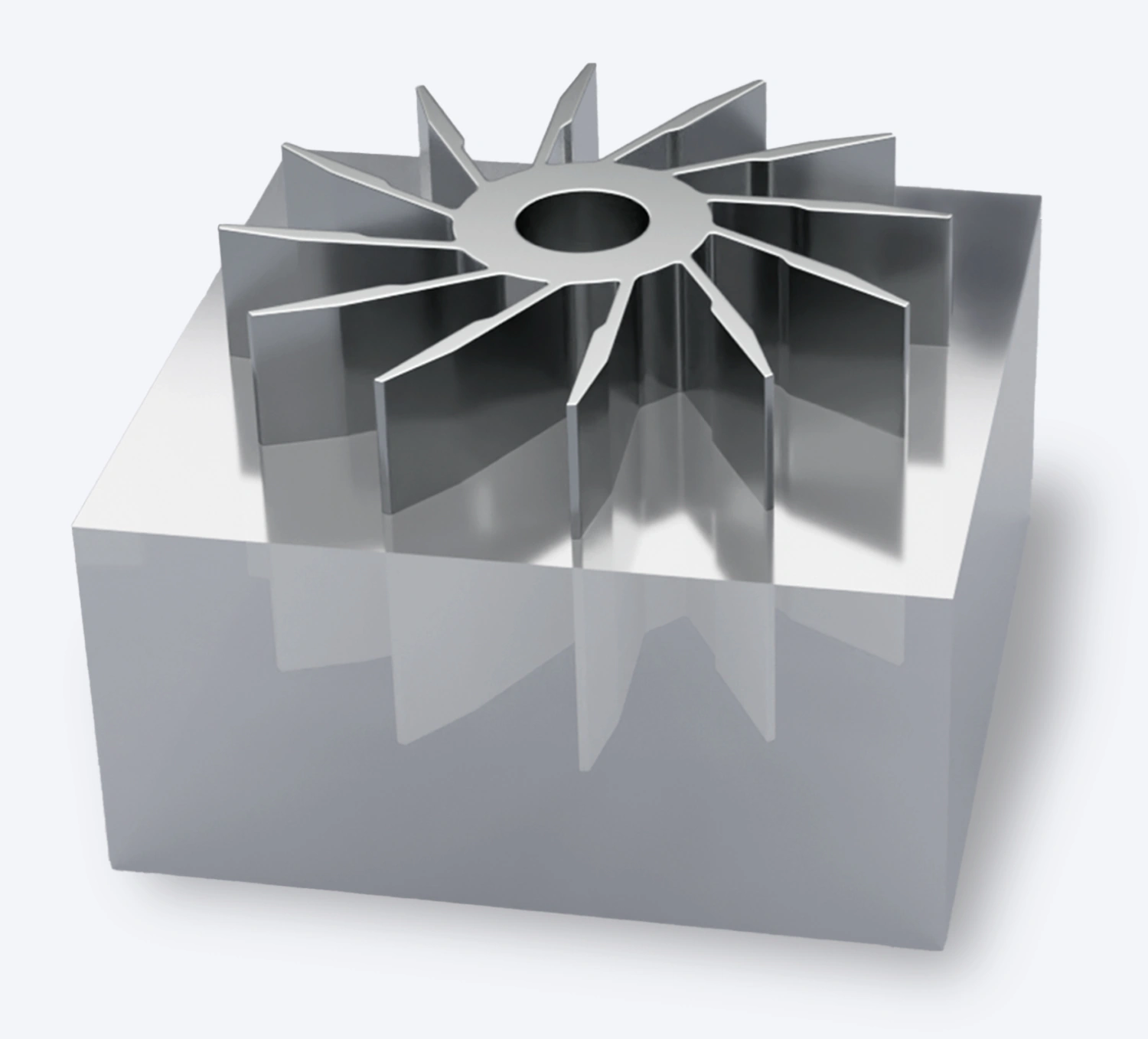
Finished Machined Part
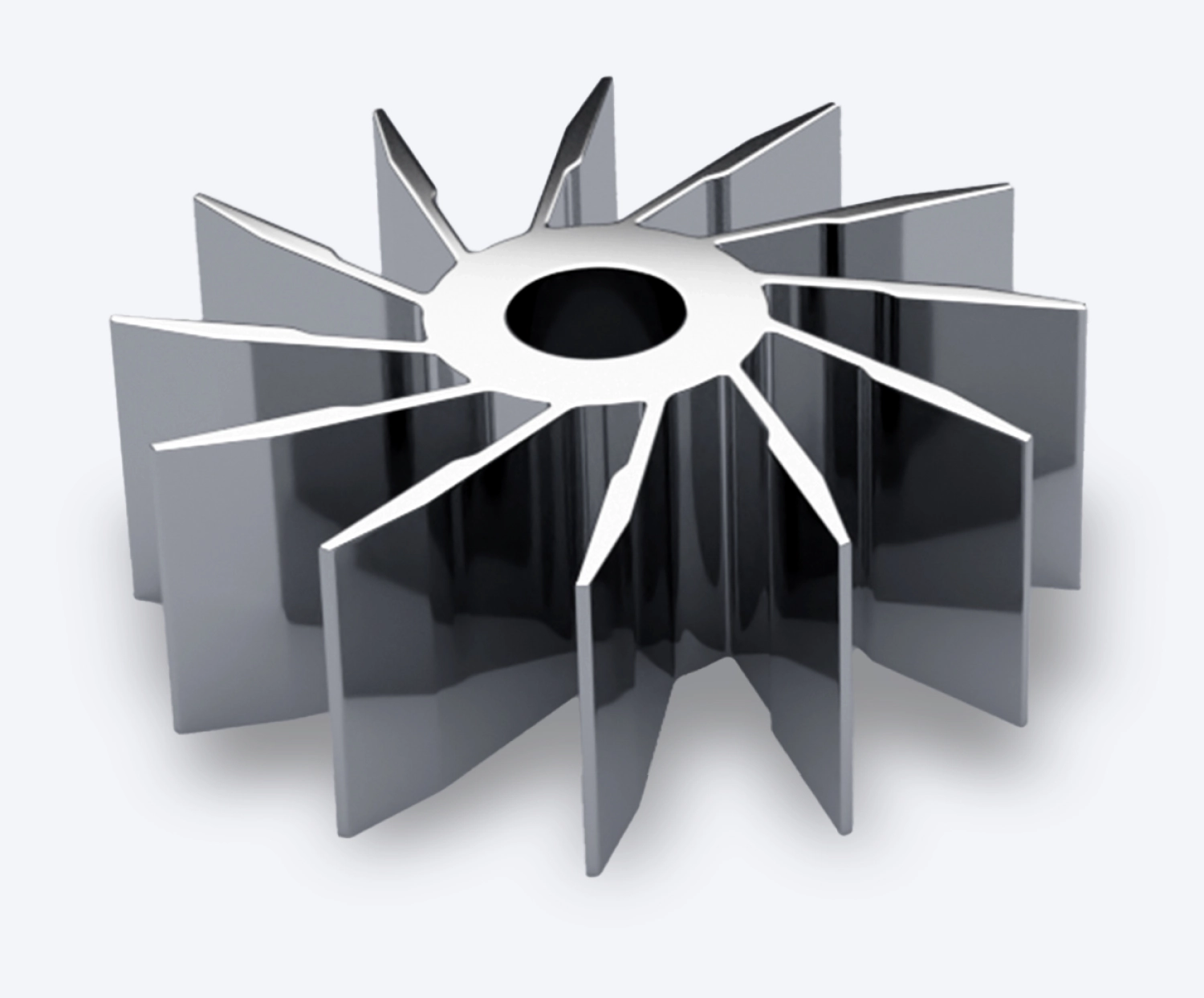
Bulk Metallic Glass
(BMG)
Raw Alloy
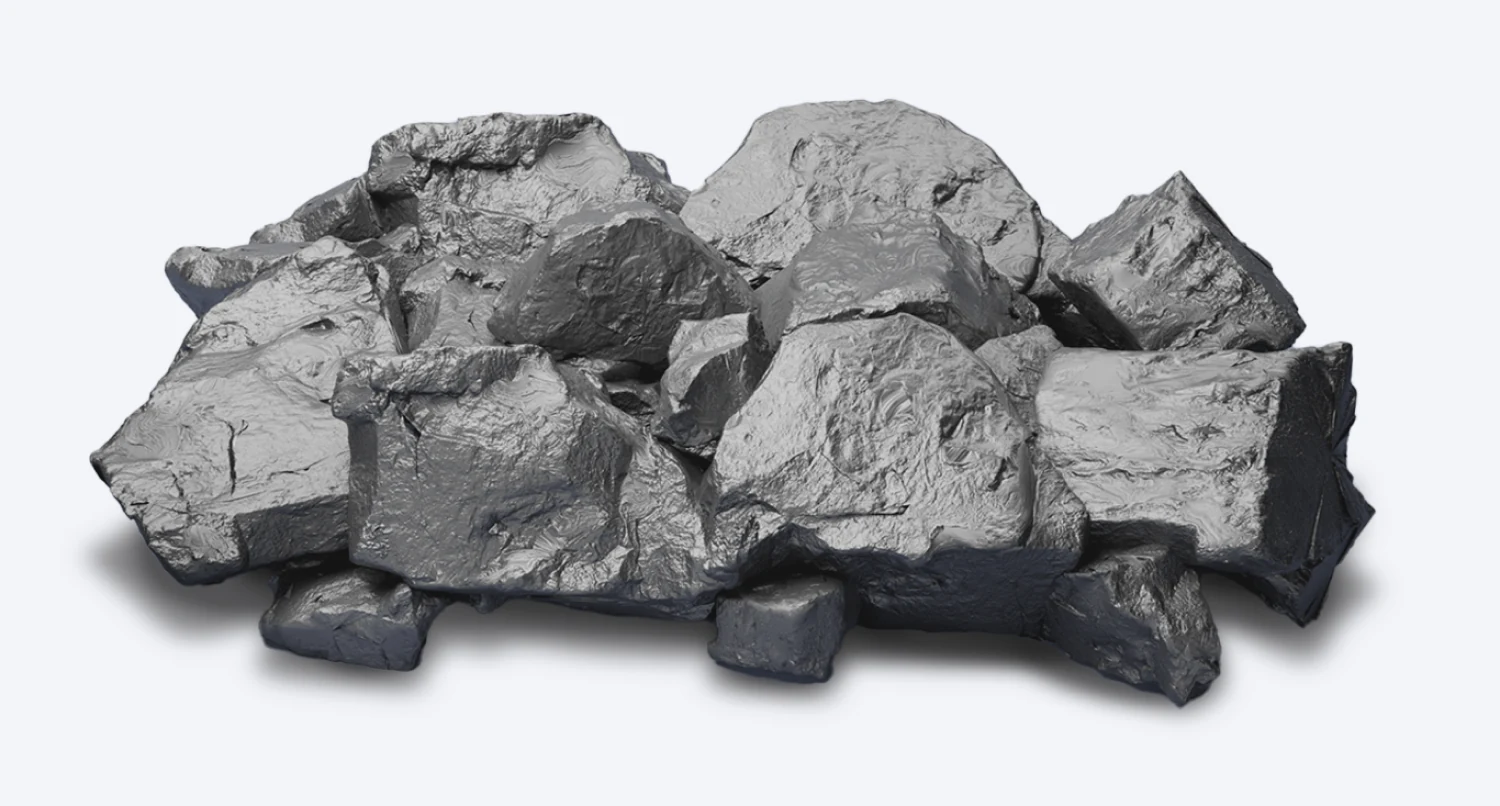
Injection Molding
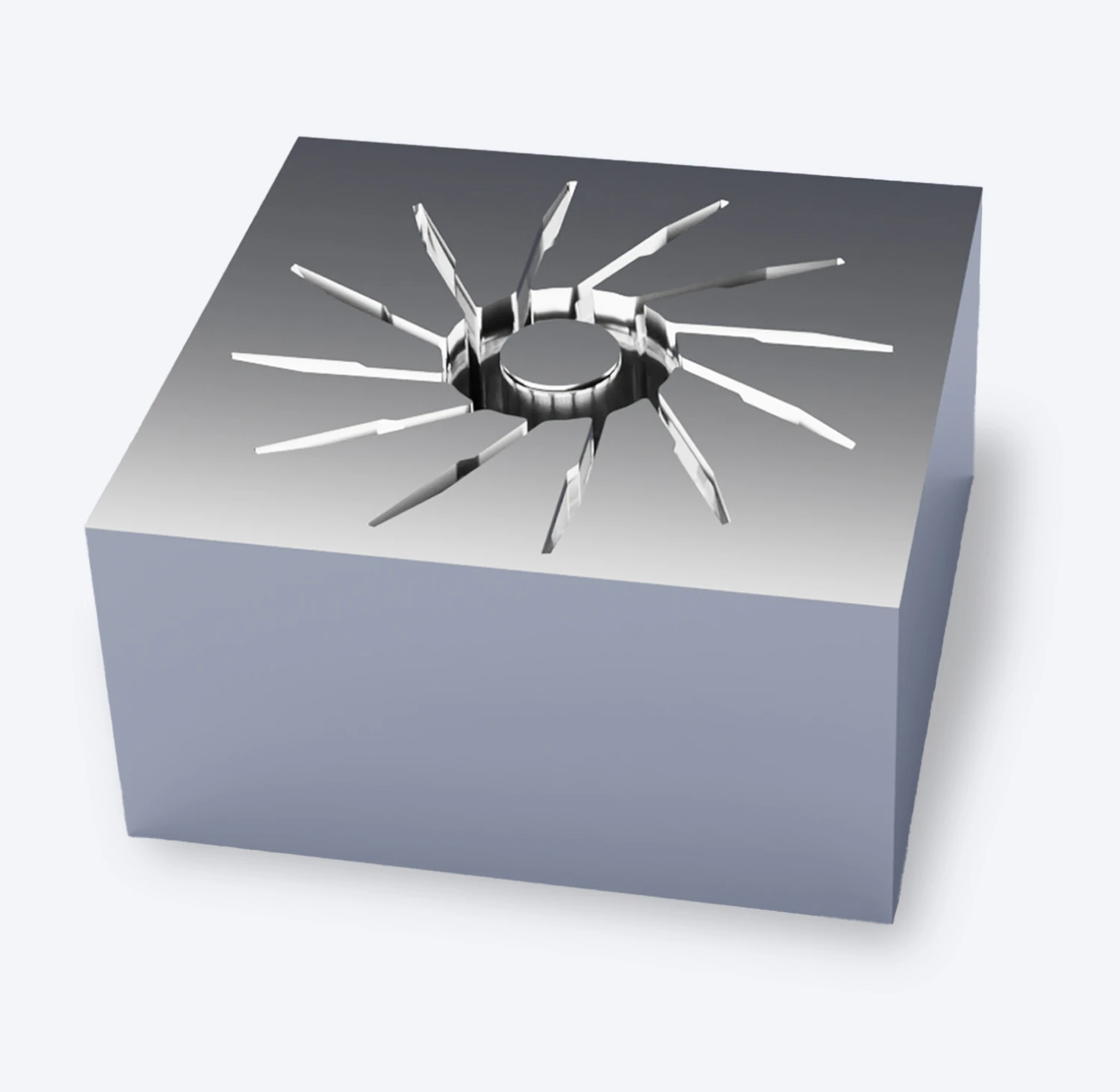
Finished Liquidmetal Part
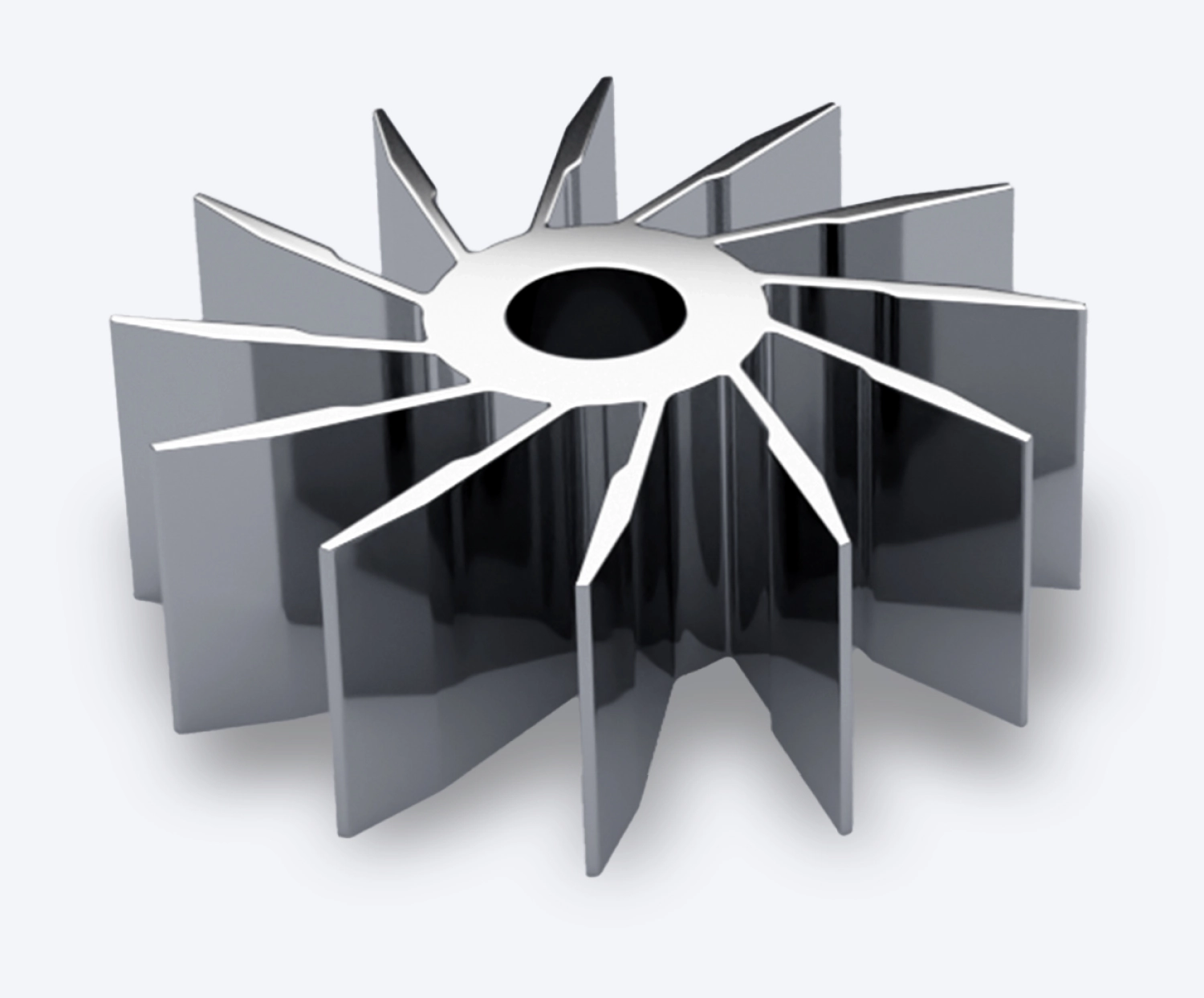
Material Properties
A manufacturing process can influence the material properties of a part due to the resulting porosity or grain structure, but the main contributor to the properties is the type of material that can be used in a particular process. The melting temperature of a material and the final part geometry will dictate which manufacturing process to use.